What is a Turret?
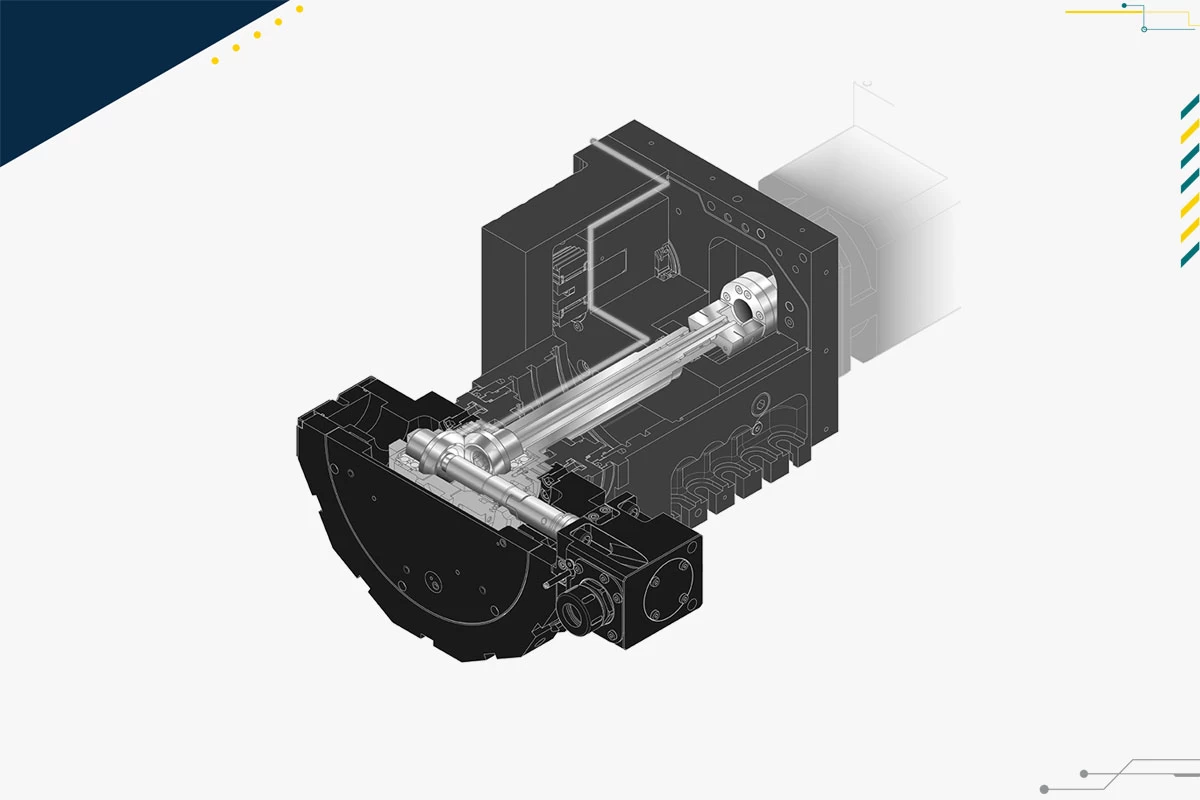
Exploring the Core Component of the CNC Machinery Industry
In the CNC (Computer Numerical Control) machinery industry, the turret is a critical component responsible for tool installation and control, significantly enhancing both machining efficiency and automation. In CNC lathes and turn-mill machines, turrets can automatically rotate tool stations to perform turning and milling operations at different angles, effectively reducing production time and labor costs. As a key player in CNC lathes, the turret plays an essential role in modern manufacturing.
I. Basic Functions and Structure of the Turret
The primary function of the turret is to enable the automatic switching of various tools, allowing CNC machines to quickly changing tools during the machining process. Most turret designs are disk-shaped with 8 to 12 tool positions, each holding a tool. Driven by either high-precision servo motors or hydraulic drives, the turret can rotate quickly and accurately to the designated tool position, reducing downtime during machining. This design provides stability and durability in high-load, high-precision machining scenarios.
II. VDI and BMT Interface Systems in Turrets
In CNC turn-mill machines, the most commonly used interface systems are VDI and BMT:
- VDI Interface System: This is a round-shank, DIN69880 standard system that is easy to install, ideal for machining tasks that require frequent tool changes, offering flexibility and good machining accuracy.
- BMT Interface System: The BMT interface fixes the tool directly through the base, reducing vibrations and deviations during machining, making it suitable for high-stability, high-cutting force machining needs. This type of turret is commonly used for machining larger workpieces, and in Asia, the BMT interface remains the mainstream choice.
III. Types and Applications of Turrets
Based on the driving method and applications, turrets are mainly categorized as follows in Taiwan:
- Servo Turret: Driven by servo motor, this type of turret controls the indexing of the tool disc through a servo motor and drive unit, achieving higher positioning accuracy and faster tool change speeds, making it D
- Driven Turret (BMT & VDI): Driven turrets adopt servo motor for tool disc rotation and tools are driven by tool drive motor. Whether it’s the C-axis, Y-axis, or sub-spindle functions, the driven turret enables turn-mill complex machining. This versatility allows complex parts to be processed on a single machine, improving machining efficiency and flexibility, making it suitable for diversified, high-precision manufacturing demands.
- Hydraulic Turret: Hydraulic turret is driven by hydraulic motor which is attached to the turret with gears. When hydraulic fluid flows through the pump/gearbox, it turns the gears one way or the other to activate the movement of the turret. With such a simple structure, it offers an economical option.

BMT Turret

VDI Turret
IV. The Importance of Turrets in Precision Manufacturing
With increasing demands for precision manufacturing, turrets play a significant role in CNC lathes and turn-mill compact machines, allowing various machining tasks to be completed on a single machine. The multifunctionality of driven turrets allow for multiple operations to be performed simultaneously, eliminating the need for frequent equipment changes, reducing turn-mill procedures, and cutting operating time. Its rigid design enhances machining stability and ensures product quality, making it particularly suitable for industries with high precision and durability requirements, such as automotive, aerospace, and medical device manufacturing.
V. Future Trends in Turret Development
With advancements in smart manufacturing technologies, turret systems are heading toward increased automation and intelligence. Automated tool change technology will become more efficient, and turret structures will be further strengthened to meet diverse material processing needs. With the introduction of adaptive control technology and AI, future turrets may evolve beyond tool holders to become intelligent systems capable of sensing conditions and automatically adjusting clamping force, feed speed, and tool angles, further enhancing machining efficiency and quality.
Conclusion
In the CNC machinery industry, continuous optimization of turret functions and structures effectively boosts production efficiency and product quality while reducing production costs. These advancements help companies maintain a competitive edge and enhance profitability in the increasingly competitive future market.
Updated: 2025/01/23