The major key for CNC Machining precision and performance : Application and efficiency improvement of Built-in Spindles
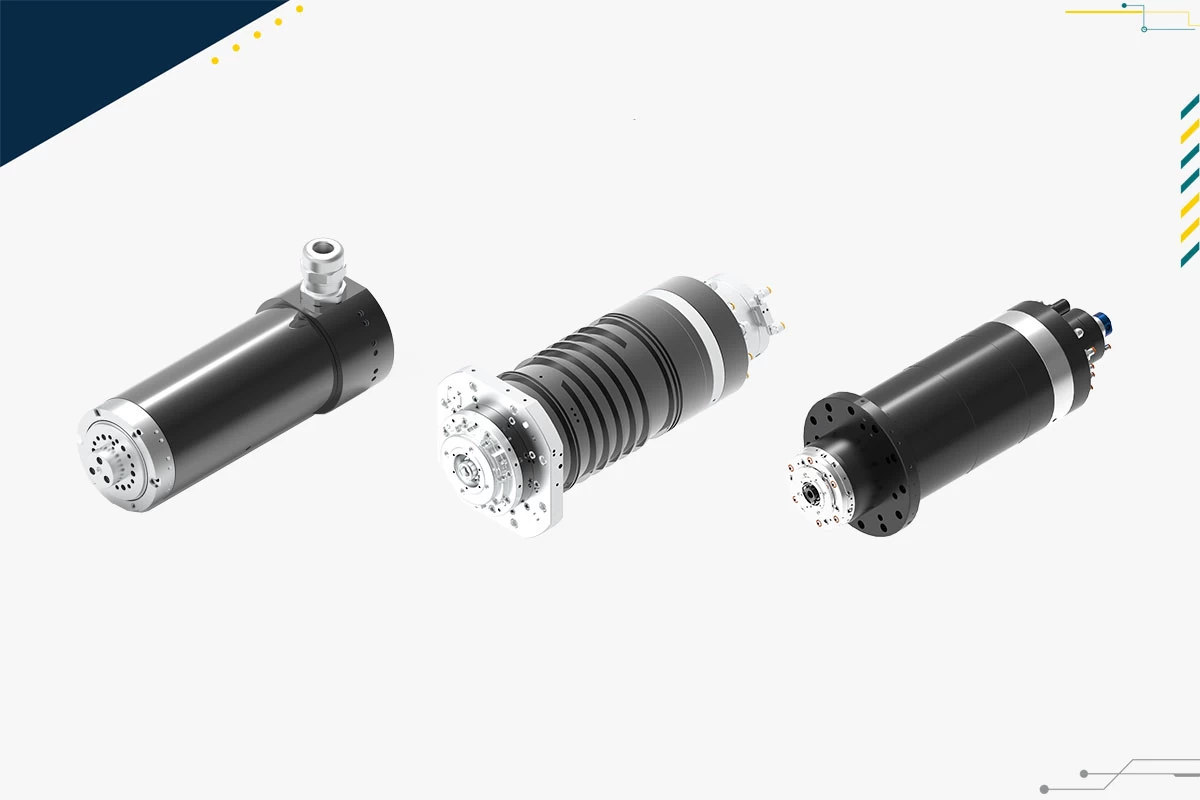
As the manufacturing industry continuously advances, CNC machining has become a core technology in modern precision manufacturing. Whether in aerospace, automotive, or electronics industries, CNC machines play a crucial role in meeting high-precision and high-efficiency machining demands. Among these machines, the application of built-in spindles is a key technology that significantly enhances CNC machining performance and precision. This article explores how built-in spindles function in turning, milling, and grinding, and how they improve the overall performance of lathes and milling machines.
Challenges and Requirements in CNC Machining
As a precise numerical control cutting technology, CNC machining faces several challenges such as:
1 Precision and Stability:
- Achieving smaller dimensional tolerances and higher surface finishes.
- External interferences like thermal deformation and vibrations can easily impact machining stability.
2 Production Efficiency:
- Reducing machining cycles and production costs.
- Ensuring stable operation and fast completion of cutting tasks.
3 Flexibility:
- Handling various types of materials and part designs, requiring machines to possess more functionalities.
Among these challenges, built-in spindles present a significant breakthrough in enhancing CNC machining performance due to their various advantages.
Technical Advantages of Built-in Spindles
A built-in spindle integrates the drive motor directly into the spindle, offering several benefits compared to traditional external type spindles:
1 Increased Rigidity and Stability:
- By eliminating transmission mechanisms like belts or gears, built-in spindles have lesser vibrations and energy loss.
- Enhances machining stability, making it ideal for high-precision applications.
2 Reduced Machining Cycle Time:
- Built-in spindles enable faster start-stop capabilities, minimizing non-cutting time during machining processes.
- Provides higher rotational speeds, suitable for high-speed cutting applications.
3 Improved Heat Dissipation:
- Integrated with high efficient cooling system inside, built-in spindles reduce thermal deformation during machining.
4 Lower Maintenance Costs:
- Eliminates the need for regular replacement of belts or gears, reducing maintenance demands.
Applications of Built-in Spindles in Grinding and Milling
The strengths of built-in spindles play important roles in grinding and milling applications:
1 Grinding Applications:
- High Speed and Low Vibration: Built-in spindles in grinding machines provide stable high-speed output while reducing vibrations, enhancing surface finish quality.
- Precision Machining: In mold manufacturing and mirror polishing, built-in spindles ensure dimensional accuracy, meeting stringent tolerance requirements.
2 Milling Applications:
- High Torque Output: Built-in spindles offer stable high torque during low-speed milling, ideal for high-strength alloys and composites.
- Versatility: Combined with CNC technology, built-in spindles enable milling machines to perform more complex operations, such as curved surface machining.
Enhancing the Performance of Lathes, Milling Machines, and Grinding Machines
Lathes, Milling Machines, and Grinding Machines are of the critical types of CNC machines, and the application of built-in spindles plays a significant role in enhancing machines performance:
1 Improved Machining Precision:
- Built-in spindles reduce transmission errors, ensuring precise spindle movement.
- Integrated sensors provide real-time monitoring of machining conditions, further minimizing errors.
2 Increased Production Efficiency:
- The faster start-stop feature of built-in spindles shortens workpiece changeover and startup time.
- Offers higher rotational and feed rates, enhancing overall production efficiency.
3 Extended Machine Lifespan:
- Integrated cooling systems lower operating temperatures, reducing component wear.
- Eliminates frequent maintenance of transmission parts, extending machine overall lifespan.
4 Reduced Noise and Energy Consumption:
- Smoother operation of built-in spindles, hence operational noise is effectively reduced.
- Enhances energy conversion efficiency, minimizing energy waste during operation.

SMG58

SMI180

SM230
Conclusion
The applications of built-in spindles not only solve multiple challenges in CNC machining but also significantly enhance the performance of lathes, milling machines, and grinding machines. The exceptional performance in turning, milling, and grinding makes the built-in spindles the corn factor for CNC machine upgrades. In the future, with continuous advancements in CNC technology, built-in spindles will further drive developments in precision, efficiency, and stability in CNC machining, creating more possibilities for the manufacturing industry.
Updated: 2025/04/17